Building Green Factory with Smart Carbon Reduction
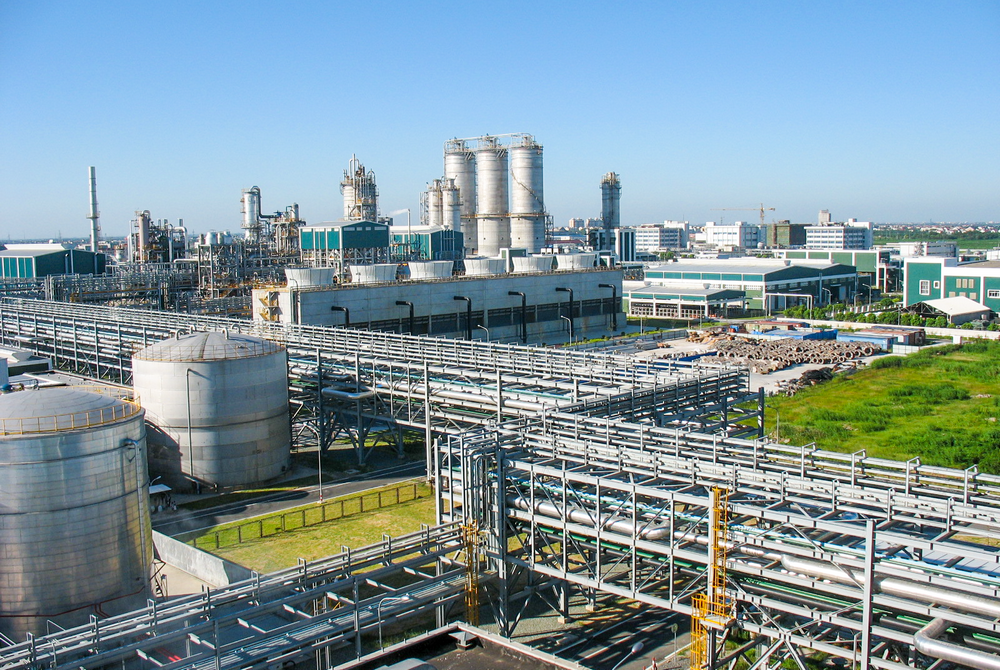
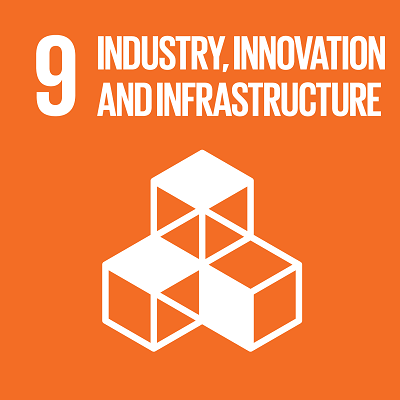
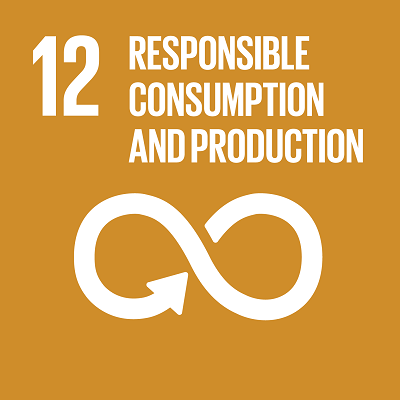
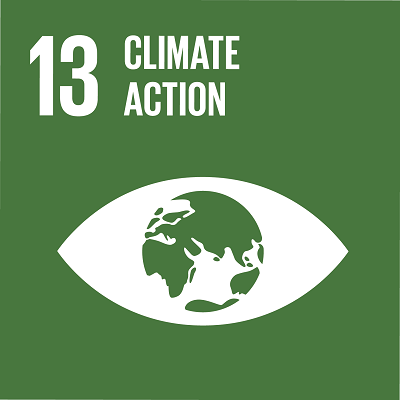
OPSC adopted ISO standards and principles of DuPont Safety Excellence since its inauguration. When production began in 2006, the plant established Energy Conservation Committee to promote energy-saving tasks and implement Regulations Governing Proposal Improvement to encourage employees to present proposals for energy conservation. In addition, the plant bettered the adjacent environment by eliminating odors, reducing noises and installing online detector for volatile organic compounds (VOCs). Corporations have the undeniable responsibility to treat industrial waste. OPSC commissions reputable waste management companies for recycling and treatment while reducing waste through avoidance. The plant has obtained multiple environmental certifications, including cleaner production evaluation in 2009; ISO 9001/14000/45001 certifications in 2010; Water-saving Enterprise in Shanghai in 2017; ISO 50001 energy management system certification and the 4th round of designation of National Green Factory in 2019. At the end of 2020, OPSC answered the government’s call for green development and launched ISO 14064-1:018 certification process on GHG inventory to strengthen carbon emission monitoring during the production cycle to track carbon footprint and enhance energy and carbon reduction.
In terms of technological development, OPSC is aided by the sophistication of an experienced team, which has been with OPSC since the very beginning. The team was involved in the plant design stage and improved upon issues often confronted in other plants. After production began, the team engaged in the optimization of production process as well as energy conservation and consumption reduction. In addition, the team improved the dry scrubber system, recycled methyl acetate and enhanced energy efficiency at the pump. These projects greatly reduced energy consumption per unit production. The team also helped incorporate AI systems such as APC, electronic permit to work (PTW) system, energy management dashboard and real time display of energy consumption per unit production. With smart inspection, data collected from the meters on-site undergo big data analysis to ensure proper operation. To enhance reliability and issue maintenance notifications in advance, the team installed online sensors on 93 critical equipment beginning in 2019 to monitor the operation in real time. The sensors successfully provided advanced warnings when irregularities occurred at the dryer and the mixer for the oxidation reactor, and prevented equipment failure and unplanned downtime. The exceptional performance has helped OPSC reach the annual governmental targets on energy consumption and intensity dual control, hence winning the title, National Green Factory.
Unity is Strength – OPSC’s Green Momentum