Retrofitting the Air Compressor System
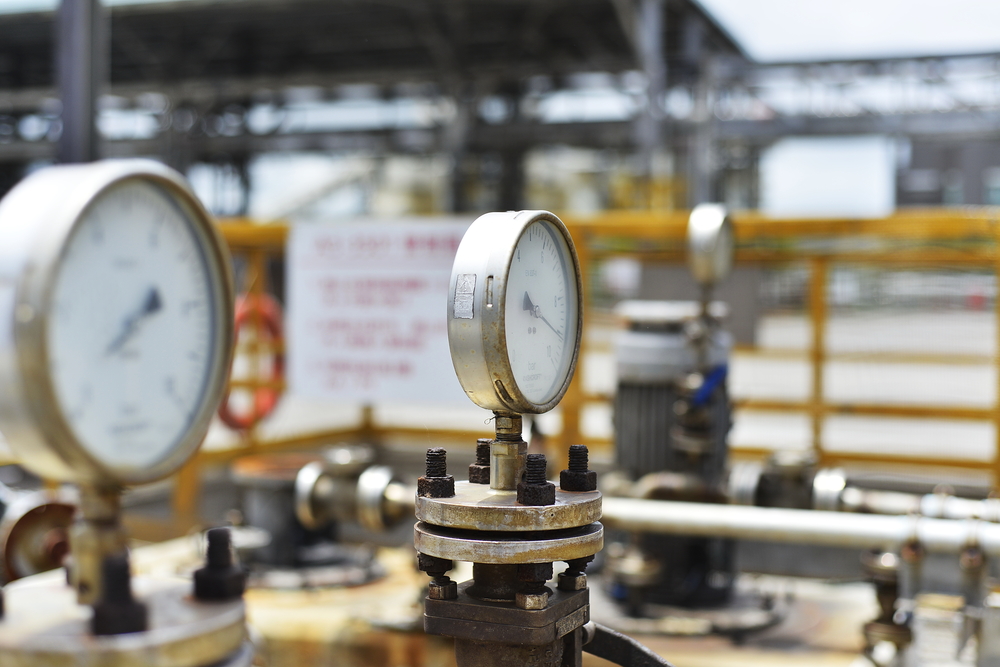
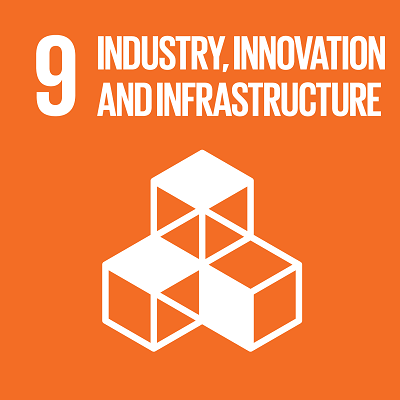
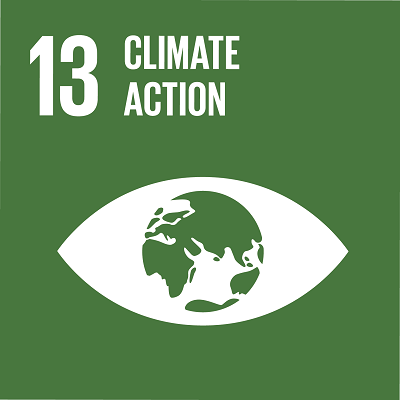
Air compressors are responsible for the majority of energy consumption at production sites, making it necessary for regular performance check and replacing with under-performing efficiency. To ensure high-efficiency operation, the air and pressure conditions must also be taken into account.
Plant 2 of OPTC puts safety first while prioritizing environmental protection and consistent production. The plant implemented a three-stage production adaptation and equipment replacement project by building the model for the cooling water system, adjusting water consumption and replacing the equipment. In February 2022, the plant retrofitted the water supply system for the air compressors. The project investment amounts to NT$20.33 million, reducing 836 GWh in electricity consumption, NT$20.89 million in electricity costs and 4,253 tCO2e in carbon emissions, reaching a 23.3% reduction rate.
The energy requirement for air compressors at Hsinpu Chemical Fiber Plant constitutes 11% of the total electricity consumption. By utilizing the online flow meter and electricity meter, the plant is able to monitor the energy consumption per unit of production for the air compressor in real time. In 2022, one of the air compressors was replaced with a newer and more efficient model, reducing electricity consumption by 188 GWh and carbon emissions by 957 tCO2e annually. Kuanyin Chemical Fiber Plant also replaced one of its air compressors with a more efficient model, reducing electricity consumption by 194 GWh and carbon emissions by 987 tCO2e annually. FEIS replaced an air compressor with a new one, improving energy efficiency by 12.7%. OTIZ also replaced the old with the new in 2022, reaching 12% in energy efficiency while decreasing electricity consumption by 23 GWh and carbon emissions by 133 tCO2e annually.